Comparer Pallet Runner🅪 aux systèmes de stockage dynamique traditionnels
Comparer Pallet Runner🅪 aux systèmes de stockage dynamique traditionnels
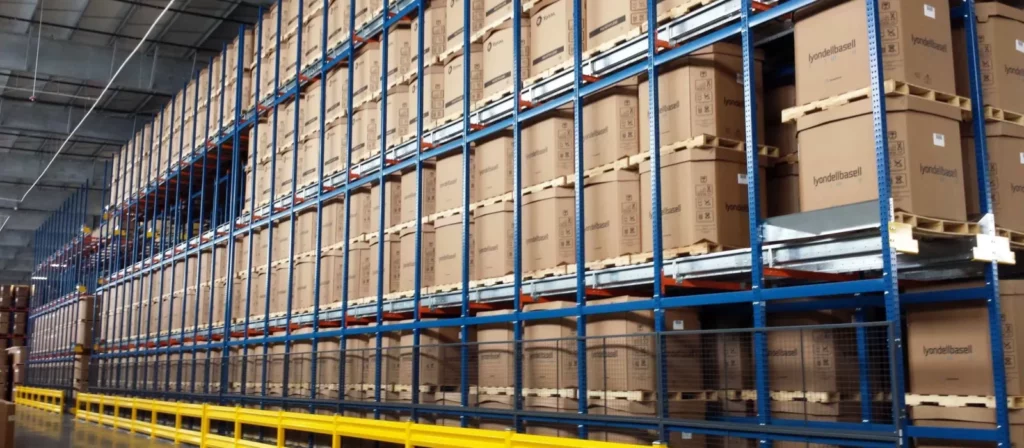
Pallet Runner🅪 versus le stockage traditionnel
Pour une gestion optimale des opérations de stockage et de déstockage de palettes en grand volume, les systèmes de rayonnages dynamiques tels que le pushback, le drive-in ou le pallet flow présentent des solutions viables pour obtenir un stockage à haute densité au sein d'un environnement d'entrepôt. Cependant, il est important de noter que chacun de ces systèmes présente ses propres limites qui doivent être soigneusement prises en compte. Dans certains cas, la mise en œuvre d'un système Solution semi-automatisée peut s'avérer être un choix plus approprié pour répondre aux diverses exigences des différentes opérations.
Il est essentiel de reconnaître que les coûts et les limites associés à chaque méthode de stockage sont distincts et doivent être évalués de manière exhaustive avant de prendre une décision. Voici une analyse de ces facteurs pour votre considération :
Drive-in | Refoulement | Flux de palettes | Solution semi-automatisée | |
---|---|---|---|---|
Flux de produits | LIFO | LIFO | FIFO | FIFO/LIFO |
Profondeur de stockage maximale** | 12 | 6 | 15 | Nombre illimité |
Sélectivité des UGS (SKU) | par baie | par allée | par allée | par allée |
Position de chargement/déchargement du chariot élévateur | drive-in | drive aisle | drive aisle | drive aisle |
Fourchette d'investissement | $ | $$ | $$$ | $$ |
Stockage et flux de produits – LIFO ou FIFO
Utilisation LIFO
Le principe LIFO (dernier entré-premier sorti) est une méthode conventionnelle de stockage des palettes, couramment employée dans les systèmes de stockage dynamique traditionnels. Toutefois, il convient de noter que si la plupart des systèmes dynamiques adhèrent au principe LIFO, les systèmes de flux de palettes fonctionnent selon le principe FIFO (premier entré-premier sorti), les systèmes Pallet Runner🅪 offrant les deux flux de stockage. Si le stockage dynamique offre un avantage substantiel en termes d'efficacité de l'espace, une limitation potentielle réside dans l'accessibilité restreinte aux palettes stockées. Avec une bonne compréhension de ce que vous stockez, de la manière dont le produit entre et sort du système de stockage, et avec les conseils d'un professionnel, ces limitations peuvent être réduites, voire éliminées.
En revanche, un système de rayonnages à palettes sélectifs ne peut pas accueillir autant de palettes, mais il garantit un accès illimité à toutes les palettes à tout moment. Cette caractéristique s'avère particulièrement précieuse dans les cas où l'accessibilité est primordiale et/ou lorsque vous stockez un petit nombre de palettes par unité de stock.
Les systèmes pushback et drive-in fonctionnent selon le principe LIFO, ce qui les rend particulièrement adaptés aux applications nécessitant un stockage en couloirs profonds. Ces systèmes s'avèrent avantageux pour les scénarios impliquant des volumes de prélèvement plus élevés mais une gamme plus limitée d'unités de stock.
L'adaptabilité du Pallet Runner🅪 est remarquable, car il peut être configuré pour fonctionner comme des systèmes FIFO ou LIFO. Dans les opérations LIFO, où le chargement et le déchargement s'effectuent dans une seule allée, les navettes à palettes sont généralement utilisées plus fréquemment.
En résumé, le choix entre les méthodes de stockage LIFO et FIFO, ainsi que la sélection de systèmes de rayonnages dynamiques ou sélectifs, dépendent d'un examen minutieux des exigences opérationnelles et des priorités d'accès. Chaque approche comporte son propre ensemble d'avantages et de limites qui doivent être évalués afin de déterminer la meilleure solution pour les besoins spécifiques de l'entrepôt. Lorsqu'une étude approfondie de ce qui doit être stocké est réalisée, il est très fréquent que la conception globale comprenne plusieurs supports de stockage.
Utilisation FIFO
Les systèmes de stockage Pallet Runner🅪 et Pallet Flow fonctionnent selon le principe FIFO (Pallet Runner🅪 peut également fonctionner selon le principe LIFO), garantissant que la première palette à être stockée est la première à être récupérée. Notamment, les deux systèmes sont conçus pour simplifier le rôle de l'opérateur/du chariot élévateur en le réduisant à la simple tâche d'accéder à la palette présentée par le système. Lors de l'utilisation de Pallet Runner🅪, des gains de productivité et d'utilisation supplémentaires peuvent être obtenus en les utilisant pour le chargement ou le déchargement complet de niveaux entiers, optimisant ainsi leur efficacité. Dans les systèmes de flux de palettes et de Pallet Runner🅪, la configuration opérationnelle nécessite la présence de deux allées : l'une, désignée pour le chargement, et l'autre pour l'accès. Cette disposition à deux allées garantit un flux rationalisé de palettes tout en maintenant la séquence FIFO.
Il est important de reconnaître que les systèmes FIFO, avec leurs composants dynamiques tels que les navettes ou les rails d'écoulement, nécessitent un entretien périodique. Toutefois, l'un des principaux avantages réside dans l'amélioration de l'efficacité des systèmes FIFO.
Profondeur des palettes
L'objectif premier de tous ces systèmes est d'augmenter la densité de stockage des palettes dans un espace restreint. Néanmoins, il convient de noter qu'il existe un compromis entre l'augmentation du stockage de palettes et l'accessibilité, particulièrement marqué dans le cas des systèmes à accumulation dynamique (drive-in). Notre analyse comparative révèle que les systèmes de flux de palettes et Pallet Runner🅪 surpassent les systèmes drive-in et pushback en ce qui concerne la capacité de stockage de palettes dans une seule allée, mettant ainsi en évidence leur efficacité supérieure en matière d'utilisation de l'espace.
En développant cette notion, les systèmes Pallet Runner🅪 apparaissent comme le summum du potentiel de stockage de palettes parmi ces méthodes. Leur avantage provient de leur indépendance vis-à-vis de la gravité ou de la nécessité d'utiliser des chariots élévateurs pour naviguer à l'intérieur du système. Cet attribut unique contribue de manière significative à leur capacité à stocker davantage de palettes par rapport aux systèmes alternatifs.
Par essence, la recherche de l’efficacité optimale du stockage des palettes consiste à trouver un équilibre entre la maximisation du volume de stockage et la garantie d'un accès facile. Les systèmes Pallet flow et Pallet Runner🅪 se sont révélés être des précurseurs et leaders dans ce domaine, caractérisés par leur capacité à accueillir un nombre impressionnant de palettes tout en contournant certaines des limites posées par les installations traditionnelles dépendant de la gravité ou des chariots élévateurs à fourche.
Sélectivité des UGS (SKU)
Plus la densité de stockage augmente, plus la sélectivité tend à diminuer. Les rayonnages sélectifs traditionnels offrent la possibilité d'accéder à n'importe quelle palette à n'importe quel moment, ce qui les rend idéaux pour gérer des stocks de faible volume et d'unités de stock importantes. En revanche, les systèmes de stockage dynamique sont conçus pour les opérations à fort volume avec un faible nombre d'unités de stock.
En ce qui concerne les systèmes drive-in, ils sont généralement limités au stockage d'une seule unité de stock par travée. L'inconvénient des systèmes drive-in est qu'ils exigent que le chargement et le déchargement se fassent de manière séquentielle, de haut en bas, ce qui se traduit par un taux d'utilisation de l'espace relativement faible, de l'ordre de 50 %.
Dans les systèmes dynamiques, chaque niveau de la baie est disponible indépendamment des autres niveaux. Les systèmes de refoulement, de flux et de navette offrent l'avantage de stocker différentes UGS dans chaque allée, ce qui améliore la sélectivité. L'utilisation disponible via ces options dépend de multiples facteurs, mais si l'on analyse correctement les UGS, les taux d'utilisation peuvent dépasser 90 %. Par conséquent, l'utilisation d'un système de stockage dynamique peut effectivement doubler le nombre de palettes stockées par rapport aux systèmes traditionnels de drive-in.
Le coût joue toujours un rôle important dans l'analyse des systèmes de stockage et, en fin de compte, il s'agit d'un investissement qui doit être examiné avec soin. Sur la base de ce qui a été décrit ci-dessus, vous devez examiner les coûts de manière plus approfondie que le simple coût initial apparent qui vous est présenté.
Exemple:
L'entreprise a déterminé en premier lieu que ses besoins de stockage étaient de 1 000 palettes, et on lui a présenté des propositions de systèmes de stockage drive-in et Pallet Runner🅪. À première vue, le système drive-in semblait nettement plus rentable que le système Pallet Runner🅪. Cependant, en procédant à une analyse plus approfondie des deux options, ils ont découvert plusieurs différences substantielles :
Positions des palettes :Compte tenu de la nécessité de stocker 1 000 palettes et de l'utilisation du système drive-in, il est apparu que l'entreprise devrait acquérir près de 2 000 positions de palettes.
Superficie en mètres carrés :Avec l'augmentation du nombre d'emplacements de palettes nécessaires pour le système drive-in, la surface requise a augmenté, ce qui a eu un impact sur l'utilisation de l'espace et sur les coûts.
Efficacité opérationnelle : Les caractéristiques opérationnelles distinctes des deux systèmes ont montré que le système drive-in nécessiterait un plus grand nombre d'opérateurs pour être géré efficacement.
Réduction des dommages :La réduction ou l'élimination potentielle des dommages causés aux produits et aux systèmes devait être prise en compte, car elle pouvait conduire à des économies et à une amélioration de l'efficacité globale.
En tenant compte de tous ces facteurs, la différence de coût initiale entre les deux systèmes s'est avérée beaucoup plus faible qu'il n'y paraissait à l'origine. Par conséquent, une évaluation complète était cruciale pour prendre une décision éclairée sur la solution de stockage la plus appropriée.
Interactions avec les chariots élévateurs
Dans les systèmes de rayonnages à palettes traditionnels tels que les rayonnages sélectifs, les rayonnages à allées très étroites (VNA) ou les rayonnages à double profondeur, les chariots élévateurs positionnent généralement la palette depuis l'allée jusqu'à l'avant du rayonnage.
Cependant, la mise en œuvre d'un système drive-in présente une différence fondamentale : l’opérateur de chariot élévateur doit entrer dans la structure du rayonnage pour stocker et récupérer les palettes. Cette façon de faire contraste avec les systèmes de navette, de refoulement et de flux de palettes, où les palettes sont commodément placées à l'avant du rayonnage.
L'entrée dans un système drive-in entraîne inévitablement des dommages potentiels à la structure du rayonnage, à la sécurité de l'opérateur et à l'intégrité de la charge palettisée. Imaginez qu'un chariot élévateur entre ou sorte d'un système drive-in avec une palette suspendue à 40 pieds dans les airs - c'est un scénario comportant nombre de risques.
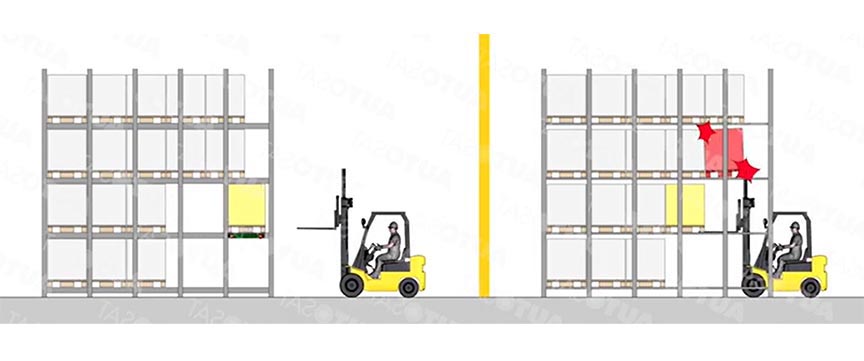
Résumé
Les systèmes de stockage dynamique, bien que plus coûteux que le stockage sélectif, s'avèrent indispensables lorsqu'une quantité importante de palettes est stockée dans l'entrepôt. Ces systèmes sont particulièrement utiles dans les lieux réfrigérés, où l'espace est précieux et doit être utilisé au maximum. Ils offrent une efficacité essentielle dans les solutions de stockage.
Voici un aperçu des différents systèmes de stockage dynamique, chacun ayant ses propres caractéristiques et ses propres coûts :
Systèmes à accumulation (LIFO) : Parmi les options les plus économiques, les systèmes drive-in ne dépendent pas de composants supplémentaires. Cependant, ils sont inévitablement endommagés et nécessitent une maintenance et des réparations régulières, ce qui risque d'annuler les économies réalisées au départ.
Systèmes à refoulement (LIFO) : Légèrement plus coûteux que les systèmes à accumulation, les systèmes à refoulement intègrent des chariots imbriqués et des composants techniques tels que des roulements. Cette complexité accrue peut contribuer à augmenter les coûts initiaux.
Systèmes à flux de palettes (FIFO) : Les systèmes de flux de palettes sont les plus coûteux de la catégorie des systèmes dynamiques à haute densité. Leur coût s'explique par l'inclusion de systèmes de rouleaux et de freinage qui s'étendent sur toute la longueur du couloir, ce qui améliore à la fois la fonctionnalité et le coût.
Systèmes Pallet Runner🅪 (FIFO/LIFO) : Les systèmes de navettes de palettes tendent à s'aligner sur le coût par palette des systèmes de refoulement. Cependant, des dépenses supplémentaires sont à prévoir en raison de l'inclusion des navettes, des besoins en énergie et de la maintenance, ce qui doit être pris en compte dans l'évaluation du coût global.
En conclusion, si les systèmes de stockage dynamique peuvent présenter un investissement initial plus élevé que les systèmes de stockage sélectif, il n'en demeure pas moins que les systèmes de stockage dynamique sont plus coûteux.
Pour plus d'informations sur la façon dont Automha Amériques peut améliorer l'efficacité opérationnelle de votre entrepôt, communiquez avec nous par courriel : americas@automha.com, ou remplissez le formulaire ci-dessous.
Steve Dale, Vice-président
Automha Americas Automation Corp.