What is a Pallet Shuttle?
What is a Pallet Shuttle?
Let’s begin by providing a comprehensive overview of a pallet shuttle system.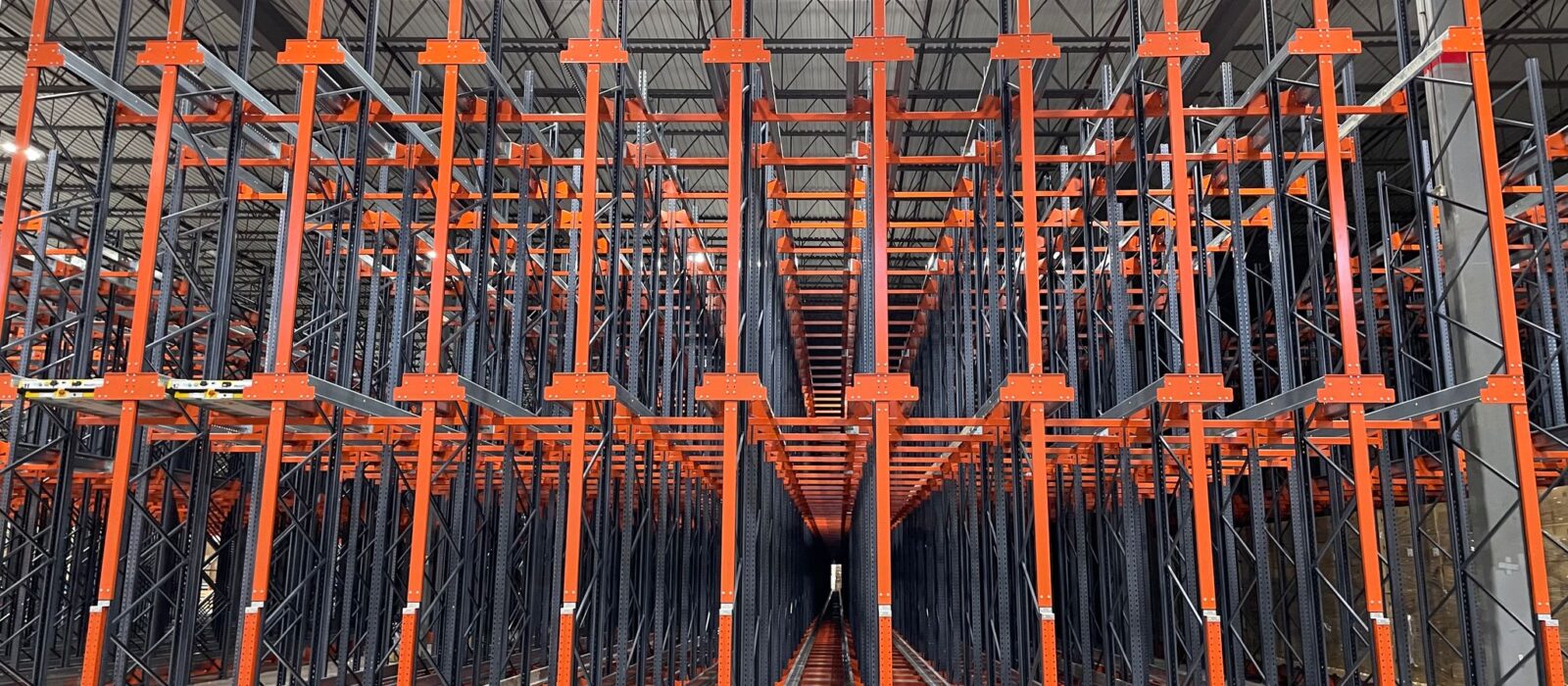
Pallet Shuttle Introduction
A pallet shuttle system represents a semi-automated solution for high-density storage, leveraging specialized “carts” (shuttles) to facilitate the seamless movement of pallets within the storage framework. Once the forklift operator has placed a cart into the designated lane, the operator can then place the pallet into the “home” (front) position. Via a handheld or truck-mounted controller, the operator can then instruct the cart to store the pallet. Widely recognized as high-density, deep lane storage, this type of system is often referred to as a “pallet shuttle” system. Alternatively, it may be identified by brand-specific monikers like Pallet Runner, pallet mole, radioshuttle, and the like.
At its essence, a Pallet Shuttle system stands as an independent high-density storage system thriving within purpose-built structures, each being configured for a specific application. These meticulously designed structures house an interwoven network of lanes, meticulously tailored to accommodate the fluid storage and retrieval of pallets. Each shuttle boasts an array of sensors, cameras, and state-of-the-art control mechanisms to ensure accurate and controlled movement and storage of palletized products.
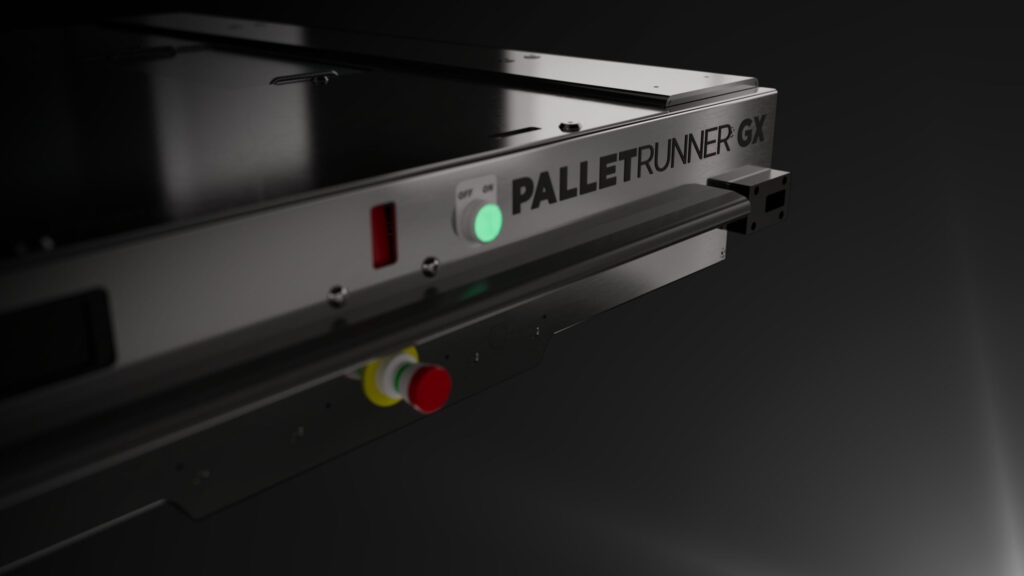
Pallet Shuttle Structure
Pallet shuttle automation provides a solution for achieving high-density pallet storage within deep lanes. As illustrated in the accompanying image, the pallet shuttle seamlessly operates within the structure that has been enhanced with rails to accommodate the specialized pallet shuttle vehicle and the palletized product it needs to store. These storage lanes exhibit remarkable potential, capable of accommodating a substantial quantity of pallets. A shuttle system can store an unlimited number of pallets deep, with clients currently utilizing up to 110 pallets deep. The depth depends on factors such as pallets per SKU, picking rates, and order profile.
Pallets find their place within the lane, maintaining a uniform and consistent spacing known as the “flue space.” The precision of pallet-to-pallet spacing holds paramount significance, owing to the dynamic and increasingly rigorous nature of building code regulations. In today’s landscape, insurance underwriters frequently mandate a steadfast 6-inch “flue” gap between pallets when opting out of in-system sprinkler utilization.
These flue spaces play a pivotal role by facilitating unobstructed vertical lines of sight throughout the entirety of the system. This strategic arrangement allows for effective water penetration emanating from the strategically positioned roof-mounted sprinkler system.
Pallet Shuttle Operation
Storage lane(s) within the system operate autonomously, with the shuttle seamlessly maneuvering between channels under the guidance of the forklift truck operator. The process is streamlined, as the operator imparts straightforward commands to the shuttle through a handheld control unit. Leveraging this interface, the shuttle discerns the required mission, and smartly maneuvers to an optimal position before executing the lifting process.
Upon depositing a pallet into a channel, the shuttle positions it precisely at a predetermined distance from its neighboring pallet. Subsequently, the shuttle automatically navigates back to the front face in readiness to accept the next load. Notably, this entire sequence transpires harmoniously while the operator simultaneously procures the subsequent pallet for loading, thus optimizing the operator’s productivity.
The shuttle cart derives its energy from an onboard, rechargeable power source in the form of a battery. Predominantly, contemporary shuttle systems harness the prowess of Lithium-ion technology. Nevertheless, there still exist older alternatives such as lead acid batteries in the market. These power sources conventionally operate at a voltage of 48V, although a subset of systems remains functional at 24V.
In accordance with the specific shuttle system, each cart mandates either one or two batteries to facilitate its operations. This aspect bears significance when evaluating aspects like charging logistics, supplementary battery acquisition, and overall ownership costs. To ensure seamless operations with minimal downtime, it is strongly advisable to procure an extra set of batteries irrespective of the chosen shuttle system. This prudent approach enables uninterrupted operation even during consecutive shifts.
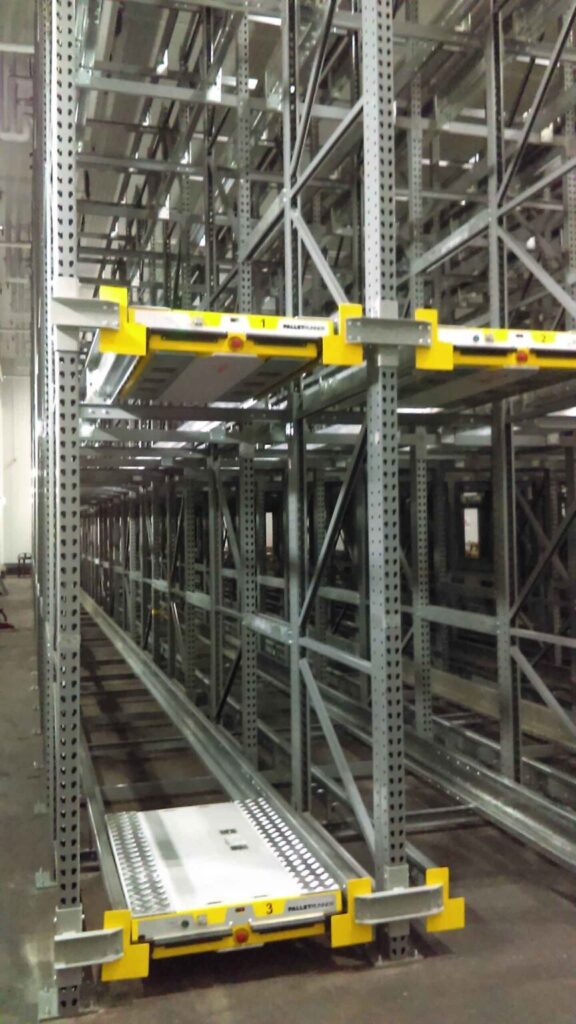