Lippert Creates More Pallet Positions
Lippert
Pallet Runner™ SolutionFrom over 140 manufacturing and distribution facilities located throughout North America, Africa and Europe, Lippert supplies a broad array of highly engineered components for the leading manufacturers of recreational vehicles, automobiles, watercraft and prefab homes. They also operate in adjacent markets, including hospitality, transportation, construction and agriculture.
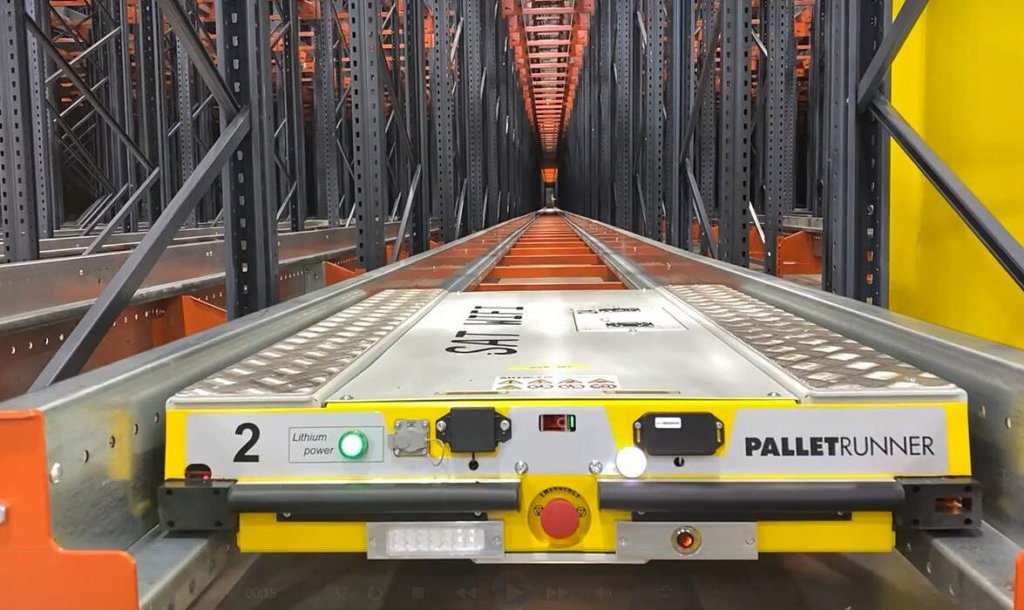
Problem
With the acquisition of one of their largest offshore suppliers, Lippert was necessary for their 900,000 square foot facility was already close to capacity. With no time, or desire to build a new warehouse and warehouse space for lease at an all time high in late 2021 and early 2022, they were running out of options quickly.
They were in need of a solution to utilize more of their available vertical space and selective pallet racking, and even solutions like push-back or drive-in pallet racking had their own challenges. One of which being safety, followed by reduced available storage space, more forklift travel aisles, and the addition of more forklifts and forklift operators.
With low SKU count and high pallet volume, keeping an inbound container of each SKU in close proximity once unloaded was also a desire for the client to help minimize the long forklift travel times with unloaded forks.
Solution
The design and implementation of one of the deepest known shuttle systems in the world with the Automha Pallet Runner™ creating simplicity and efficiency for their large-scale cross docking operation.
At 110 pallets deep and 3 levels high, Automha took what would have used almost 500,000 square feet of double stacked floor space with a maze of forklift aisles and condensed it down to just over 163,000 square feet providing the client with 23,100 pallet positions in a rather small footprint.
Advantages
With the implementation of Pallet Runner™, the client saw several operational gains outside of just dense storage.
- Reduce forklift travel both with loaded and unloaded forks
- Reduced forklift fleet
- Simplified cross dock operations
- Reduced cost per square foot by utilizing the available vertical space
- Reduced pallet costs by changing from a double stack pallet to a single, taller pallet
- Freed up floor storage space to bring product from other facilities reducing cost at surrounding plants