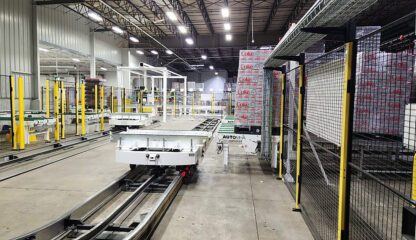
Autosatmover System Case Study
Before their introduction to the AutoSatMover System, a confidential Coca-Cola bottler and distributor faced the challenge of optimizing their production…
Pallet Runner™ GTR is the newest generation of the industry’s leading Pallet Runner™, designed and produced exclusively by Automha. Founded in 2001, Pallet Runner™ has an estimated 11,000 units operating worldwide. It is chosen by global manufacturers such as Coca-Cola, Pepsi, Red Bull, Nestle, and Kellogg. Pallet Runner™ GTR is the number-one choice for some of the largest integrators.
Download BrochureSpeeds up the handling process and cuts labor costs, and offers remarkable flexibility; accommodating different inventory management styles to optimize warehouse operations.
Pallet Runner™ GTR deep lane storage continues to provide our clients benefits over more conventional storage mediums – increasing utilization, in some cases, by up to 50%!
Pallet Runner™ GTR is the simplest automation to design and integrate into a company’s day to day operations. It also provides a company a good introduction to warehouse automation.
Pallet Runner™ GTR is equipped with the latest technology, allowing you to transform your warehouse operations, maximize space, improve operator efficiency, and create a safer working environment. Pallet Runner™ GTR has a cart for over 20 applications, and is compatible with most cart and pallet shuttle manufacturers
Before their introduction to the AutoSatMover System, a confidential Coca-Cola bottler and distributor faced the challenge of optimizing their production…
They were in need of a solution to utilize more of their available vertical space and selective pallet racking, and even solutions like push-back or drive-in pallet racking had their own challenges.
How deep aisle pallet storage lanes with Pallet Runner™ increased space utilization rates with this FIFO system.